After engine oils, hydraulic oils are the second most important group of lubricants. They account for approximately 15% of total lubricants consumption. In 1998, mineral – based hydraulic oils accounted for approximately 80 - 85% of all hydraulic oils in Germany.
Modern hydraulics can be divided into three principal areas there by making special demands on its components and the hydraulic medium. In recent years, the performance of hydraulic systems has increased significantly. This is reflected in higher pressure, higher system temperature, and lower system volumes, which increase circulation and thus stress on the medium.
Hydraulic fluid developments today and in the future depending on their correct application, are of enormous economic significance. Optimum applications save energy, reduce maintenance intervals, reduce wear, increase machine life, and thus enable worthwhile savings. |
|
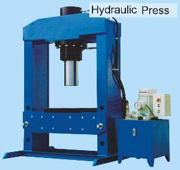 |
|
HYDRAULIC OILS |
Hydraulic oils are now available with exceptional stability towards oxidation. They are prepared from carefully selected base oils by special refining treatment and their natural stability is improved still further by the incorporation of oxidation inhibitors.
Another requirement to be considered is that hydraulic oil must protect the system from corrosion or rusting. That the components of the system are at all times flooded with oil is no safeguard against corrosion unless the oil itself is non-corrosive. Experience has shown that only highly refined oils of high oxidation stability remain free from corrosive acidity for long periods. However, rusting is liable to occur, irrespective of whether the oil is fresh or in a state of degradation, if the ferrous surfaces of the system are in contact with moisture and air entrained in the oil. The oil therefore, must have good metal-wetting properties and must be able to maintain a protective film over the surfaces of the system. Oils incorporating a special rust inhibitor can provide good protection against rust.
With the advent of modern hydraulic systems it has become necessary for the hydraulic fluid to have special antiwear properties. Oils have been developed having high load carrying capacity, besides having excellent thermal and oxidation stability.
A special requirement for machine tools with very slow moving tables lubricated from the hydraulic systems is that the lubricant should be able to prevent stick-slip or jerky motion on the table. This requirement can be met by the use of special additive. |
|
HYDRAULIC OILS |
|
Lubol Pressoil 15
Lubol Pressoil 22
Lubol Pressoil 32
Lubol Pressoil 46
Lubol Pressoil 68
Lubol Pressoil 100
Lubol Pressoil 150
Lubol Pressoil 220
Lubol Pressoil 320
Lubol Pressoil 460 |
|
|
High quality solvent refined mineral oils
Containing antioxidant, antiwear, antirust and antifoam additives. |
|
|
|
|
|
APPLICATION : |
Hydraulic equipments in control and power transmission systems requiring antiwear properties.
Also suitable for oil cooled rotary compressors. |
|
BENEFITS : |
Better corrosion resistance additives to prevent rusting and corrosion of machinery.
Proper viscosity based grades fulfill the requirements of hydraulic pumps and designed systems.
Ability to protect the system against corrosion and rusting.
Separate readily from water resulting in reduced corrosion of various system parts.
Outstanding oxidation stability thereby providing long oil service life.
Very good antifoam / air release property thereby avoiding erratic operation.
Compatible with all normal mineral oil seal materials. |
|
MEETS PERFORMANCE STANDERD : |
IS 10522 :1983
IS 3098:1983
DIN 51 524 Part I HL Type
These grades are recommended for hydraulic plants,compressor,pumps and machinery tools. |
|
LUBOL PRESSOIL HLP |
These are the premium grade oils possessing thermal and oxidation resistance properties, it posses anti foam characteristics, antiwear properties and posses a very high stable viscosity index. These oil have a good chemical stability to ensure long and smooth life .It also posses the special characteristics of antifoaming thus ensuring the smooth functioning of machinery.
Lubol Pressoil HLP 32
Lubol Pressoil HLP 46
Lubol Pressoil HLP 68 |
|
MEETS PERFORMANCE STANDERD : |
LUBOL PRESSOIL HLP
IS 11656:1986(MARCH 202)
DIN 51 524 PART 2-HLP TYPE
Denison HF-0 & HF-2 |
|
SPECIFICATION : |
LUBOL GRADE |
K.V. cSt @ 40 °C |
Viscosity
@100°C |
Viscosity Index |
Flash Point COC, °C |
Pour Point °C |
FZG Pass
Load Stage |
Lubol Pressoil 15 |
13.9 |
3.3 |
106 |
170 |
- 9 |
- |
Lubol Pressoil 22 |
22.6 |
4.4 |
106 |
175 |
- 9 |
- |
Lubol Pressoil 32 |
32.6 |
5.5 |
101 |
190 |
- 9 |
10 |
Lubol Pressoil 46 |
47.6 |
7.1 |
100 |
220 |
- 9 |
10 |
Lubol Pressoil 68 |
67.6 |
8.7 |
98 |
230 |
- 9 |
10 |
Lubol Pressoil 100 |
97.9 |
11.0 |
96 |
240 |
- 9 |
10 |
Lubol Pressoil 150 |
146.9 |
14.6 |
95 |
250 |
- 9 |
10 |
Lubol Pressoil 220 |
212.8 |
18.3 |
95 |
270 |
- 9 |
- |
Lubol Pressoil 320 |
311.9 |
23.5 |
95 |
285 |
- 9 |
- |
Lubol Pressoil 460 |
492.2 |
31.7 |
95 |
300 |
- 9 |
- |
Lubol Pressoil HLP 32 |
32.6 |
5.4 |
99 |
210 |
- 21 |
10 |
Lubol Pressoil HLP 46 |
48.4 |
6.9 |
98 |
240 |
- 18 |
10 |
Lubol Pressoil HLP 68 |
67.9 |
8.6 |
98 |
240 |
- 18 |
10 |
|
|
Page 2 |