The lubrication of machine tools is described in DIN 8659-1 and -2 and ISO 5169 and ISO 3498. These standards contains requirements which should be observed when manufactures and users establishing lube plans. These also satisfy the requirements specified in DIN/ISO5170 (machine tools lubrication system) Lubrication plans should cover all the components in a machine tool which need lubrication. These should describe : |
The precise location of all lubrication points.
The type of lubrication required.
The lubricant itself according to DIN 8659 – 1 and -2 and ISO 3498 and the tank volume and the lubrication time table. |
The purpose of a lubricating plan as part of routine servicing is to ensure that a sufficient quantity of the correct lubricant is applied to the right point at the right time (VDI Guideline 3009). Machine manufactures normally supply lubricants recommendation tables with machine on the basis of this information, a maintenance plan is created for every machine which shows the type of lubricant and the lubrication interval. For most machines, a maintenance plan and a lubrication chart are included in the service hand book. Machine manufactures often refer to the lubricant recommendation issued by component manufactures. The recommendation issued by the manufactures of hydraulic components, gearboxes, slide ways, and linear guides must be observed. |
|
|
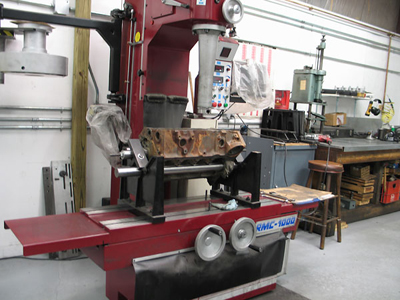 |
|
|
LUBRICATING PROPERTIES |
Oil is generally considered to be more effective lubricant since the main function of lubricating oils are to maximize oil film strength, offer high chemical stability, resistance to wear corrosion, formulation of deposits oxidation etc. These qualities are obtained by the addition of selected additives to the base oil blends. The viscosity required for any given set of conditions depends on size speed, load, and temperature of the bearing. Mineral oils of high quality should be chosen so as to obtain efficient lubrication of moving parts.
The method used to apply the oil depends mainly on the running speed of the bearing. Use of proper method is especially important with high-speed bearings, which are liable to overheat through churning of the oil if it is not correctly applied. The following means of application are suitable : |
:: Oil bath and splash systems - low and medium speeds.
:: Circulating systems - medium speeds. |
Over-lubrication should be avoided. As a general guide, with oil baths, it can be taken that the oil level should not be above the centre of the bottom-rolling element when the bearing is not rotating. |
MESHNOL OILS |
|
This oil is primarily recommended for machines lubricated on total loss systems. They are High quality
solvents with high viscosity index. These oils are also recommended for spindle bearing machines lubricated on total loss system. They provide a good oil film and prevents to rusting and corroision. |
|
RANGE |
VG : 15, 22, 32, 46, 68, 100, 150, 220, 320, 460
|
|
APPLICATION: |
- Bearings used at mild or medium operating conditions requires lubrication.
- Lubricating system applies where straight mineral oils would suffice.
|
BENEFITS |
- Perfect lubrication for wide operating temperatures.
- Long oil shelf life.
- Prevents corrosion.
|
|
MEETS PERFORMANCE STANDERD: |
Meshnol 15 to Meshnol 460 grades (Specification for machinery oils).
|
|
STROAGE AND HANDLING |
 |
- Indoor storage is preferred for lubricants.
- Barrels should be stored off the ground away from water surface.
- Barrels should be positioned horizontal with the bungs at 3 0'clock
and 9 0' clock position to ensure that the bungs are kept in contact
with oil during storage.
|
|
SAFETY |
Good standards of industrial and personal atmosphere should be maintained. |
|
|
|
|
SPECIFICATION : |
LUBOL GRADE |
K.V. cSt @ 40 °C |
Viscosity
@100C |
Viscosity Index |
Flash Point COC, 0C |
Pour Point0C |
Meshnol 15 |
14.4 |
3.05 |
103 |
168 |
- 6 |
Meshnol 22 |
22.8 |
4.54 |
103 |
172 |
- 6 |
Meshnol 32 |
32.5 |
5.50 |
102 |
182 |
- 6 |
Meshnol 68 |
66.98 |
8.68 |
101 |
214 |
- 6 |
Meshnol 100 |
100.68 |
11.41 |
100 |
240 |
- 6 |
Meshnol 150 |
152.20 |
14.78 |
98 |
240 |
- 6 |
Meshnol 220 |
224.00 |
18.52 |
91 |
250 |
- 6 |
Meshnol 320 |
331.00 |
23.70 |
94 |
257 |
- 6 |
Meshnol 460 |
462.2 |
28.8 |
95 |
270 |
- 6 |
|
|