|
METAL WORKING OIL |
|
The great flexibility and versatility of the different types of machining method are particularly significant in the metal working industries. Although for some years now there has been growing trend towards non-cutting (forming) methods for work piece quality reasons and to save material and process costs, this has still not had any obvious effects on the volume share of lubricants. This is also apparent from the machine tools statistics. The dramatic changed prophesied in the nineteen seventies did not take place in the nineteen eighties and nineties.
Because of the particular significance of cooling for the cutting operation, this process is called cooling lubrication and the fluids used are called coolants. Apart from this term “Coolant” which is commonly used in general practice, there are also numerous others. terms for specific application such as cutting oils, grinding oils, reaming oils, deep hole drilling oils and honing oils |
|
MACHING OF METALS |
- Water Based Cutting Fluids (Soluble Cutting Oils)
- Neat Cutting Oils
|
The following points concerning the storage and use of soluble oils are important. |
|
STORAGE |
Exposure of packages to moisture or to excessive heat or cold should be avoided. |
|
Preparation of Emulsion |
|
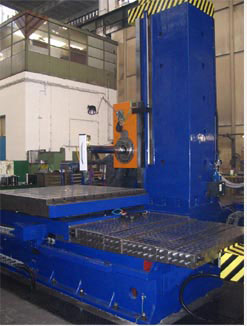 |
|
|
The oil concentrate must be added to the water (remember: oil = Oil in last). |
- Measure the water into a clean tank.
- Measure the required volume of concentrate and gradually pour it into the water. Keep mixing while pouring. Slow-speed mechanical agitation is preferred.
- Use a suitable mixing unit or proportioner.
- Verify concentration after mixing.
|
Note: |
Hard water reacts with soaps to produce scum, and with cutting fluids to break down the emulsion. It is recommended that hard water be treated prior to preparation of the emulsion.
- It is very important to measure the concentration after mixing. This can be accomplished by using a refractometer or drop kits, or by sending a sample to a test facility.
|
Proper care and handling of cutting fluids involves several important factors, including storage, mixing, checking the concentration of soluble oil emulsions (using refractometers), pH (using a pH meter), filtering the particulates by centrifuging, bacteria control, tramp oil control(hydraulic oil leaking into the cutting fluid system), application to the cutting zone etc. A variety of problems can occur with respect to cutting fluid performance. In some cases the fluid may require to be changed completely. |
|
|
|
|
|
WATER BASED CUTTING FLUIDS |
|
|
|
|
LUBOL – CUTNOL - N |
Soluble cutting oil is a combination of mineral oil, petroleum additives and emulsifier, when water is added in an oil, the stable milky emulsion is formed. It has an objectionable odour and it also causes staining & discoloration. |
MEETS PERFORMANCE STANDERDS: |
Meets : IS:1115-1986 |
APPLICATION: |
Used at water to oil ratios between 25:1. |
|
 |
|
|
LUBOL CUTNOL BN
This is a premium quality oil blended from refined base stocks,additves and emulsifiers.These oils forms stable emulsion with water useful for all applications requiring a soluble oil where sight of workpiece is important.This is suitable for all metals and for all machining operations where emulsion based lubricants are preferred.Emulions are prepared with the additon of oil into water with a vigorous proper stirring.The strength of emulsion is maintained with the addition of oil at the time of production.
MEETS PERFORMANCE STANDERDS:
Meets : IS:1115-1986
BENIFITS:
Suitable for high emulsion stability with hard water .
Better surface finish with increased tool life.
|
SYNTHCUT SS : SEMI SYNTHETIC CUTTING FLUID |
SYNTHCUT SS is a unique combination of lubricity additives, rust preventive chemicals, wetting agents and boundary lubricants resulting in a truly biostatic metal working coolant. Biostatic fluids provide only minimum nutrient sources for microbial growth. The result has greatly extended sump life with virtual elimination of biocides and other tank side additives. SYNTHCUT SS contains exceptional lubricity properties making it an ideal choice for use with steel, stainless and aluminum alloys in operations from moderate to high severity. Semisynthetics are essentially a hybrid of
Soluble oils and synthetics. They contain small dispersions of mineral oil, typically 2 to 30 percent, in a
Water-dilutable concentrate. The remaining portion of a semi-synthetic concentrate consists mainly
of emulsifiers and water. Wetting agents, corrosion inhibitors and biocide additives are also present.
Semisynthetics are often referred to as chemical emulsions or preformed chemical emulsions since the
Concentrate already contains water and the emulsification of oil and water occurs during its production.
The high emulsifier content of semi synthetics tends to keep suspended oil globules small in size,
decreasing the amount of light refracted by the fluid. Semi synthetics are normally translucent but can vary
from almost transparent (having only a slight haze) to opaque. Most semi synthetics are also heat
sensitive. Oil molecules in semi synthetics tend to gather around the cutting tool and provide more lubricity. As the solution cools, the molecules redisperse. |
|
ADVANTAGES |
Like synthetics, semi synthetics are suitable for use in a wide range of machining applications
And are substantially easier to maintain than soluble oils.
They provide good lubricity for moderate to heavy duty applications.
They also have better cooling and wetting properties than soluble oils, allowing users to cut at higher speeds and faster feed rates . Their viscosity is also less than that of a soluble oil thus providing better settling and cleaning properties.
Semisynthetics provide better control over rancidity and bacterial growth, generate less smoke and oil mist (because they contain less oil than straight or soluble
Oils), have greater longevity, and good corrosion protection.
Disadvantages. Water hardness affects the stability of semisynthetics and may result in the formation of
Hard water deposits. Semisynthetics also foam easily because of their cleaning additives and generally
offer less lubrication than soluble oils. |
|
SYNTHCUT |
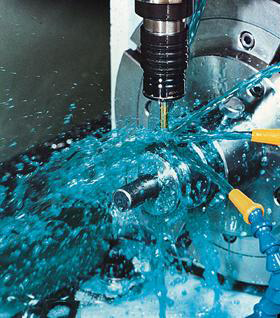 |
Machining and grinding fluids are designed for use on all metals, plastics, glass and composites. These products are engineered to provide total performance, whether running in small individual sumps or large central systems. Formulated using today's leading chemical technologies and qualified raw materials, they contain balanced lubrication chemistries to provide optimum results. In addition, our products deliver outstanding biostability properties, corrosion protection, post-processing synchronisity, low or no foam and complete aqueous compatibility. Synthetic fluids contain no petroleum or mineral oil it generally consist of chemical lubricants and rust inhibitors dissolved in water. Like soluble oils, synthetics are provided as a concentrate which is mixed with water to form the metalworking fluid. These fluids are designed for high cooling capacity, lubricity, corrosion prevention, and easy maintenance. Due to their higher cooling capacity, synthetics tend to be preferred for high-heat, high-velocity turning operations such as surface grinding. They are also desirable when clarity or low foam characteristics are required. Due to their wet ability, good cooling and lubricity, emulsifiable synthetics are capable of handling heavy-duty grinding and cutting operations on tough, difficult-to-machine and high temperature alloys The appearance of emulsifiable synthetic fluids ranges from translucent to opaque.
LUBOL Synthcut also provides a full line of mist and saw lubricants for "near dry" applications. These eco-based fluids are formulated by utilizing natural vegetable base stocks and additives. LUBOL Synthcut – is a Synthetic type coolant intended for use on ferrous metals and its chemical formula is angled to overcome any difficulties in the cutting and grinding of Cast Iron with soluble media. A reliable small amount of EP additives is present so that a high surface finish can be achieved. Lubol Synthcut is ideally suited for machining and grinding of Cast Iron. They are the right choice for production grinding where wheel grains must cut continuously without any trace of burn marks. These products can be used for light duty machining operations |
|
ADVANTAGES |
SYNTHCUT fluids have the following qualities which contribute to superior service life
Excellent microbial control and resistance to rancidity for long periods of time.
Nonflammable, nonsmoking and relatively nontoxic.
Good corrosion control.
Superior cooling qualities.
Greater stability when mixed with hard water.
Reduced misting problems; and Reduced foaming problems. |
|
Synthetics are easily separated from the workpiece and chips, allowing for easy cleaning and handling of these materials. In addition, since the amount of fluid clinging to the workpiece and chips is reduced, less makeup fluid is needed to replace coolant lost to drag-out.
Good settling properties allow fine particulates to readily drop out of suspension, preventing them from recirculating and clogging the machine-cooling system. Overall, synthetics are easier to maintain due to their cleanliness, they offer long service life if properly maintained and can be used for a variety of machining operations. |
|
|
DISADVANTAGES |
|
Synthetics are less prone to problems associated with oil-based fluids.
Moderate to high agitation conditions may still cause them to foam or generate fine mists.
A number of health and safety concerns, such as misting and dermatitis, also exist with the use of synthetics in the shop.
Ingredients added to enhance the lubricity and wettability of emulsifiable synthetics may increase the tendency of these fluids to emulsify tramp oil, foam and leave semi-crystalline to gummy residues on machine systems.
Synthetic fluids are easily contaminated by other machine fluids such as lubricating oils, thus it and needs to be monitored and maintained so as to be used effectively . |
|
SPECIFICATION : |
PETRO GRADES |
Emulsion Test, 400ppm Hard Water |
Cast iron Corrosion (No. of pits/area of staining- intensity of staining) |
Froathing Test,200ppm
hard water |
K.V. cSt @ 40 °C |
LUBOL –CUTNOL - N
LUBOL – CUTNOL - BN
SYNTHCUT SS
SYNTHCUT |
No oil/No cream
No oil/No cream
Golden Yellow
Blue |
0/0-0
0/0-0
0/0-0
0/0-0 |
No froth
No froth
No froth
Nil |
28 – 32
24 – 30
10 – 12
7 – 9 |
|
|
|
|
QUENCHING OILS |
These oils are blended from High Viscosity Index Base Stocks having good oxidation and thermal stabilty,good fluidity and low Volatility.Some of these oils are blended with special additives or selected polar compounds to meet specific requirements.These oils are used for quenching operations on a vide variety of steel parts such as nuts,bolts,ball bearing,speed tools etc.It meets specifications of quenching oil.
The petroleum based medium finds the widest application in comparison to water or synthetic based quenchent.They are easy to control and give equal and symmetrical stiffness.It is suitable for large scale automotives and it is non toxic and non corrosive in nature.
RELIQUENCH series have been prepared from a refined base stock formulated with special additives and posses the following characteristics.
Good thermal properties.
High fire point and high flash point.
High boiling point and high volatility.
Good chemical and oxidation stability.
RELIQUENCH 110
This oil has been specially designed for quenching of components especially parts. RELIQUENCH 110 is best suitable in all the places where low quenching level is prepared. It does not posses any specific additives.
PERFORMANCE LEVEL;
MEETS IS SPECIFICATION 2664-1974
RELIQUENCH 111
This is a blend of refined petroleum oil consisting of fatty acids of high grade. It posses a good wetting characteristics and has a higher quenching speed. It is recommended for high quenching operations.
MEETS PERFORMANCE STANDERDS:
MEETS IS SPECIFICATIN 2664-1980
RELIQUENCH 112
This is a special grade quenching oil which acts as a best medium fo transferring heat and has a good dispersant characteristics. It is is best for its application in high grade products such as automotive greases transmission components, dyes and tools.
MEETS PERFORMANCE STANDERD:
MEETS IS 4543-1977
SPECIFICATION :
Product |
K.V. cSt @ 40 °C |
Flash Point |
GM Megnative
Quenchochrometer |
Pour Point |
RELIQUENCH 110
RELIQUENCH 111
RELIQUENCH 112 |
28
22.6
28 |
190
180
175 |
27.9
24.6
20.6 |
--
-3
-- |
|
|
METCUT OILS |
METCUT 95 |
These oils are blended from high refined base stocks containg fatty oils and sulphur compounds to impart extreme pressure additives.These oils are recommended for multipurpose neet cutting tools.These oils are used without adding any type of dilutes and hence increases the life of tools and machineries.These oils can be applied in all ferrous and non ferrous metals.
METCUT 100
These are the specialized metal working fluids. The use of this special oil for CBN grinding brings the following advantages for the user.It enables the user to filter to a very fine degree using precoated filter, which has a favourable effect on both the surface finish of the components and the trail life of the grinding.
METCUT 105
This is a special lubricant recommended in those places where deep hole drilling techniques are employed mainly in the arnament industry where “GUN DRILLING” operations are preferred. Thus METCUT 105 plays a decisive role as a coolent additives. The main function of METCUT 105 is to reduce the friction between the abrasive material and the surface of the workpiece in the contact zone thus increases the tool life of the grinding wheels.
|
|
SPECIFICATION : |
Product |
K.V. cSt @ 40 °C |
Saponification
No. mg KOH/g |
Flash Point
PMCC. °C |
Sulphur |
METCUT 95
METCUT 100
METCUT 105 |
35
12
13.5 |
13
-
- |
166
185
150 |
Active
Active
Active |
|
FERCUT OILS |
LUBOL offers a comprehensive line of neat oils that helps to extend tool life for application ranging from light duty cutting to heavy duty broaching. These products are blended from high viscosity index base stocks and contains fatty material which posses supremacy over other oils. Select grades offer high performance in both high speed grinding operations as well as for special applications such as manufacturing of cemented carbide tools. Fercut fulfills conman operation demand such as high lubricity, longer tool life ,light color, low odour, reduced oil mist while maintaining an excellent HSSE profiles. It does not stain yellow metals. It is a tri purpose oil for cutting, machine lubrication and hydraulic applications.
|
All machining operations on non-ferrous metals. |
Machining of ferrous metals where the
severity of operation is not high.
Addition of chlorine enables the use of these oils
for extreme pressure – low/moderate temperature
cutting operations where feed rates are high but
speeds are low.
These operations include gear hobbing, screw
cutting, tapping, milling, reaming etc.
|
ADVANTAGES |
Minimize welding of the chip to the cutting tool. |
- It helps to retain sharpness of the cutting edge and
reduces stress at the cutting point.
- It reduces friction between chip and tool face
thus generate less heat.
- It does not stain non-ferrous metals.
- It posses special chlorinated based additives for its application as a multipurpose neat cutting oil.
|
|
Health & Safety |
These oils are unlikely to present any significant health or safety hazard when properly used as recommended . Application and good standards of industrial and personal hygiene are maintained. |
|
|
SPECIFICATION : |
Product |
K.V. cSt @ 40 °C |
Saponification
No. mg KOH/g |
Flash Point
PMCC. °C |
Sulphur |
FERCUT 20
FERCUT 22
FERCUT 32 |
20.1
22.1
32.4 |
4.1
2.5
7.5 |
157
166
167 |
Inactive
Inactive
Inactive |
|
|
MEETS PERFORMANCE STANDERD: |
IS 3065 : 1985 [ reaffirmed march, 2002 ] (for METCUT 95) |
|
HONLE 7X |
During grinding the honing tool has grit bonded multiple cutting edges. The most important grain material are corundrum, diamond etc.
During honing, there is a very large contact zone between tools and work pieces with relatively low pressure. The honing oil is kept at a constant temperature by chillers and these oils are of very low viscositiesThese oils have an excellent cooling effect.. Special inhibitors in the honing oil can prevent the sulphur from dissolving during honing, stone bonding and the material to be machined. |
|
SPECIFICATION : |
Product |
K.V. cSt @ 40 °C |
Saponification
No. mg KOH/g |
Flash Point
PMCC. °C |
Sulphur |
HONLE 3X |
20.1 |
4.1 |
157 |
Inactive |
HONLE 5X |
22.1 |
2.5 |
166 |
Inactive |
HONLE 7X |
32.4 |
7.5 |
167 |
Inactive |
|
|
|
|
|
|